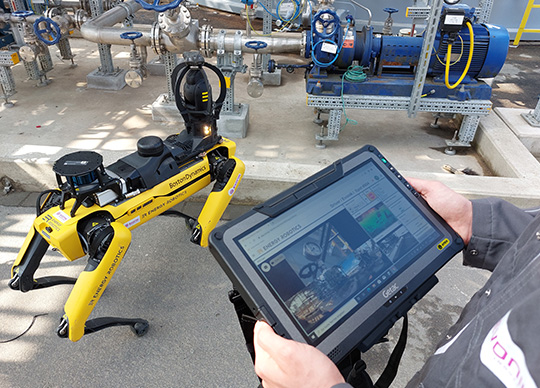
Conducting maintenance and inspection tasks in critical areas using an autonomous robot is being carried out by Evonik as part of a project with three partners at one of its company-owned chemical plants.
The aim of the project is to evaluate the practicality of an automated robotic maintenance and inspection solution in the chemical industry. The robot’s primary task is to travel along pre-programmed inspection routes, collecting important operational data. It will also conduct automated safety inspections that cannot be integrated into a remote maintenance concept (or only at great expense). Organisations can then use data collected to improve the intervals between inspections while simultaneously increasing asset reliability.
Getac’s tablet plays a pivotal role in the project, serving as the main interface between robot, control software, and human operator. For control and monitoring in the plant, the operator can access the software via the F110-EX, while an additional controller is used for quick interventions during operation.
Thorsten Schimpf, process expert, Evonik, said, “The robot receives its orders through the Getac F110-EX, which can also be used to control it during corresponding missions, such as in the tank farm. The robot is equipped with sensors, as well as infrared and optical cameras, allowing it to navigate to specific locations within the facility and take photos of displays or record data, which can then be transmitted back for evaluation. For effective operation, we knew we needed a portable rugged device with enough power to display video feeds from the robot in real-time. The F110-EX allows us to do just that.”
The requirements for the F110-EX tablet are high. Not only must it be highly robust and ATEX-certified, but the screen must also be easy to read outdoors, under a wide range of environmental conditions including rain, and it must be fully functional in both hot and cold temperatures.
Evonik also required a Windows operating system as well as the ability to capture and process large amounts of data both quickly and effectively. Connectivity and performance play a key role as well, allowing for fast video transmission and play back. In addition, an long-term evolution (LTE) connection is required because there is no wireless local area network (WLAN) in the tank farm. Finally, Bluetooth is needed to connect the controller to the tablet. With the appropriate Getac carrying strap, the F110 can be carried comfortably in front of the body, so the user has both hands free to operate the controller at the same time.
Thorsten Schimpf said, “Evonik not only recognised Getac as a good solution, but Getac responded immediately to our enquiry, was able to help quickly, and offered the right solution for our needs. The F110-EX is extremely reliable and fail-safe, it works flawlessly and meets our very high requirements for performance, functionality, and connectivity. We are very satisfied with the F110-EX.”
Eric Yeh, managing director, Getac Technology GmbH, said, “The Getac F110-EX is based on state-of-the-art rugged technologies, making it ideally suited to Evonik’s ambitious project. We are very pleased to be able to contribute to the project’s success and look forward to working closely with Evonik on similar initiatives in the future.”