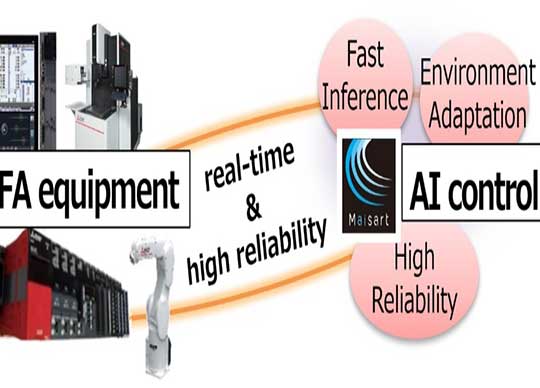
Mitsubishi Electric Corporation and the National Institute of Advanced Industrial Science and Technology (AIST) have announced they have developed an AI technology that predicts changes during automated manufacturing processes and then makes real-time adjustments in the factory-automation (FA) equipment, such as motion speeds, etc., during operation. In addition to eliminating the need for time-consuming manual adjustments, the AI estimates the confidence level of inferences regarding factors such as machining error and then controls the FA equipment based on suitable levels of confidence.
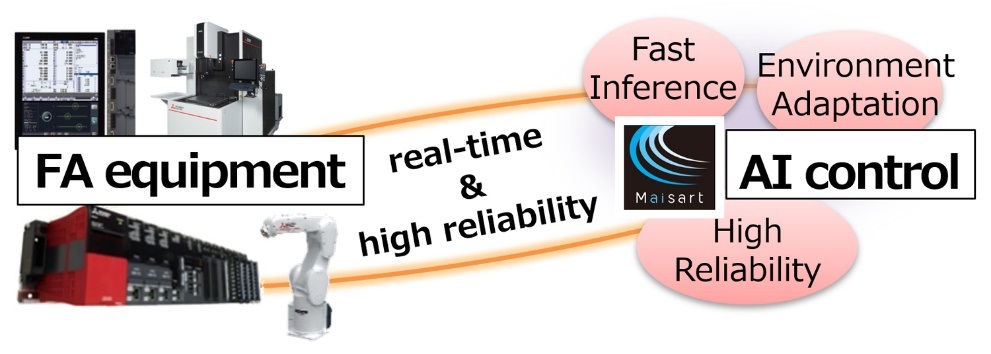
AI technology for real-time control of FA equipment during operation
Key Features
1. FAST: AI ACHIEVES HIGH-SPEED INFERENCES FOR DYNAMIC CONTROL OF FA EQUIPMENT CONTROL
In factories that use FA equipment for agile manufacturing, such as computerized numerical controller (CNC) cutting machines and industrial robots, the movements, operating speeds, acceleration, etc. of the equipment vary during the operating processes. In conventional manufacturing, skilled workers must
adjust the operating parameters according to various specifications, such as the required level of accuracy. Mitsubishi Electric has now developed an AI technology that simultaneously performs high-speed inferences and equipment control for realtime FA operation. Incorporating Mitsubishi Electric’s expertise as an FA equipment manufacturer, the new low-load AI control technology performs inferences while simultaneously controlling FA equipment. Although the technology minimizes its processing load, it is capable of achieving high-level inference accuracy while simultaneously guiding FA equipment control.
2. ADAPTABLE: IN-PROCESS LEARNING TO ADAPT TO CONSTANTLY CHANGING WORK FACTORS
The shapes of workpieces change during manufacturing and this can lengthen manufacturing times or lower processing quality. In addition, changes can vary by workpiece, making it difficult for FA equipment to learn in advance. Mitsubishi Electric’s new technology, however, allows the AI to learn work factors during FA equipment operation and then make real-time adjustments as needed. In addition, the technology formulates physical phenomena, such as friction, and then incorporates these mathematical expressions to enable learning during operation, making it possible to adapt to constantly changing processing factors.
3. RELIABLE: AI PERFORMS ADJUSTMENTS ACCORDING TO INFERENCE-CONFIDENCE LEVELS
AI inferences must be reliable to ensure that real-time control of FA equipment leads to stable product quality and efficient processing. Mitsubishi Electric’s new algorithm calculates the confidence level of inferences by learning the machine characteristics of each process and each target device. By using
this algorithm to control FA devices, the new AI ensures high reliability.
EXAMPLES OF AI CONTROL TECHNOLOGY APPLICATION
1. FAST INFERENCES
As an example of the high-speed inference of Mitsubishi Electric’s AI control technology, the company developed a solution to estimate loads on robotic arms. Various load parameters are utilized to calculate acceleration and deceleration speeds, for which the AI function quickly infers load values using information about the robot, such as motor current, joint angle, etc. Simultaneously, the confidence levels of the inferences are calculated. Finally, acceleration and deceleration are adjusted based on estimated values and confidence levels. To evaluate the effectiveness of this technology, a validation test was
conducted to compare differences in robot motion when using and not using load inferences. As shown in Fig1-2, robot operation time was confimed to be reduced by 20% when inferences were used. Moreover, more stable operation was achieved by adjusting robot motions only when the confidence level was high.
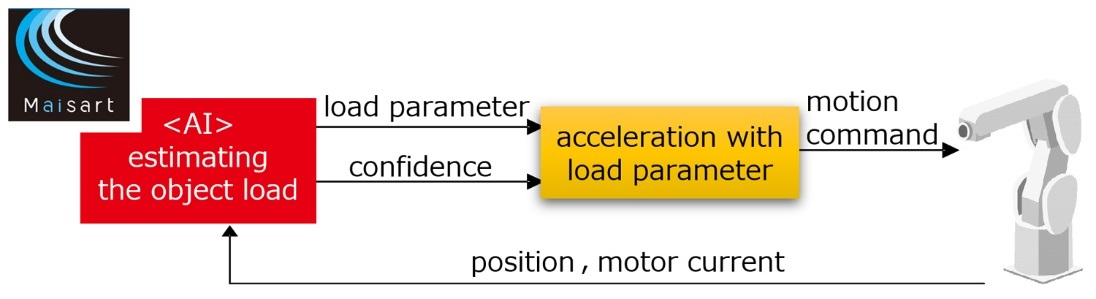
Image: Fig. 1-1 Using AI to estimate load and confidence levels
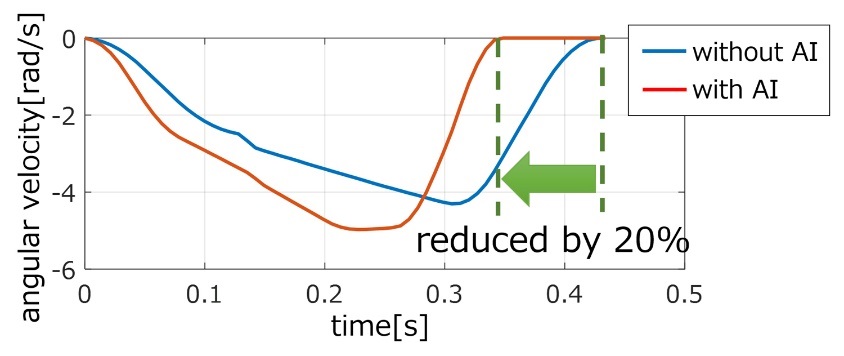
Image Fig. 1-2 Faster opertion using load estimation
2. ADAPTATION TO CHANGING CONDITIONS
As an application example of Mitubishi Electric’s AI control technology that adapts to changing processing conditions, the company developed a solution for automatically adjusting an engraving EDM (electric discharge machine). The EDM positions an electrode close to the workpiece and generates an electric discharge to perform engraving. Debris produced during machining, however, must be ejected with the electrode, and the amount of debris increases as processing proceeds, so the frequency of debris ejection must be increased. In the new solution, AI learns state of debris ejection that is produced and then
automatically adjusts the frequency of ejection Tests have confirmed that machining time is reduced up to 23% compared to processing without AI adjustment.
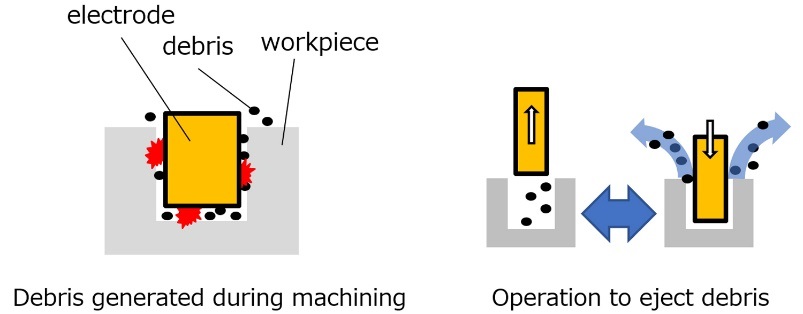
Image: Fig. 2-1 Machining with an engraving EDM
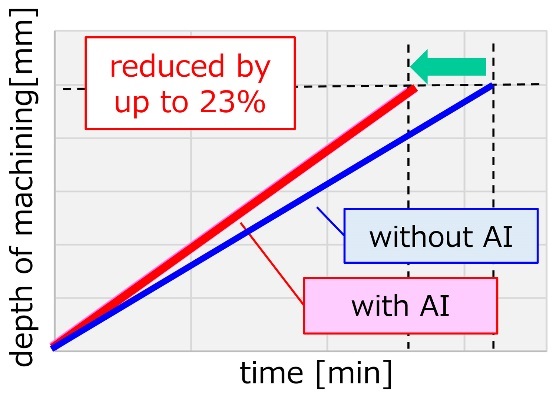
Image: Fig. 2-2 Processing with & without AI
3. RELIABILITY
As an example of the reliability of Mitsubishi Electric’s AI control technology, the company developed an AI error-correction solution for CNC cutting machines. The AI estimates constantly changing machining error, or the difference between the cutting machine’s current position and the command value, to enable correction even during dynamic machining. Also, the confidence levels of the AI’s error inferences are indexed to ensure that error correction is performed only if the confidence level is suitably high. Tests confirmed that machining accuracy is improved by 51% compared to using error correction not
supported with AI. Furthermore, low confidence levels can be improved through relearning.
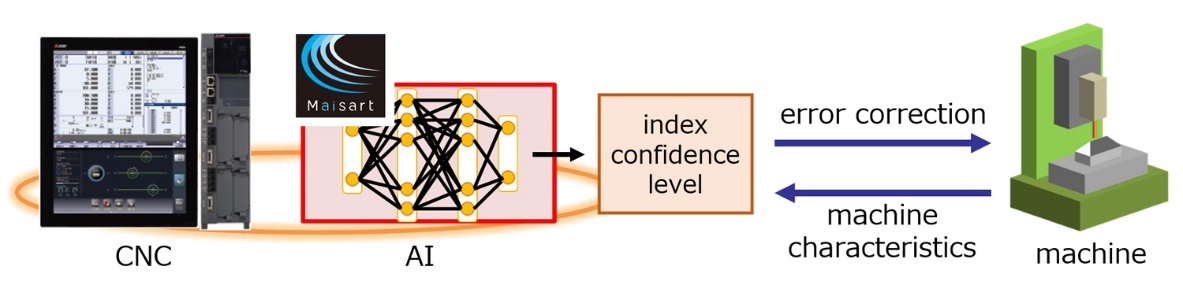
Image: Fig. 3-1 AI error correction in CNC cutting machine
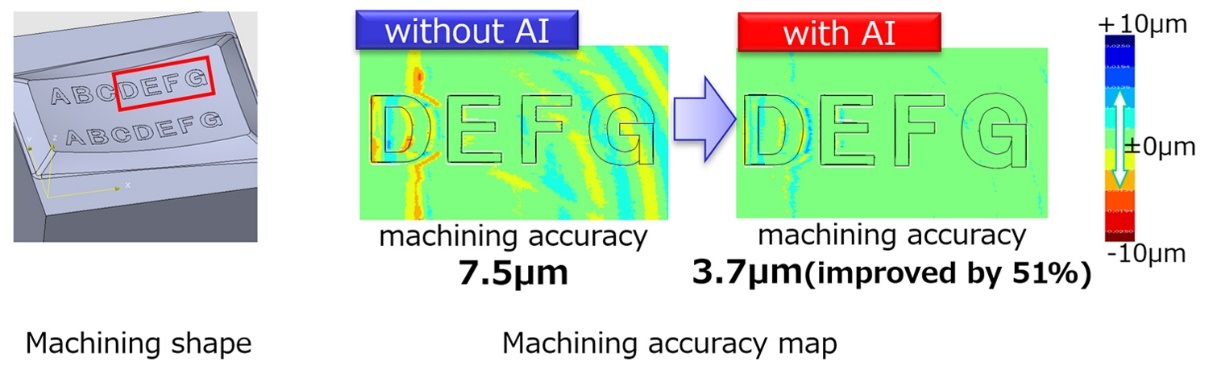
Image: Fig. 3-2 Better results with AI-supported CNC cutting machine